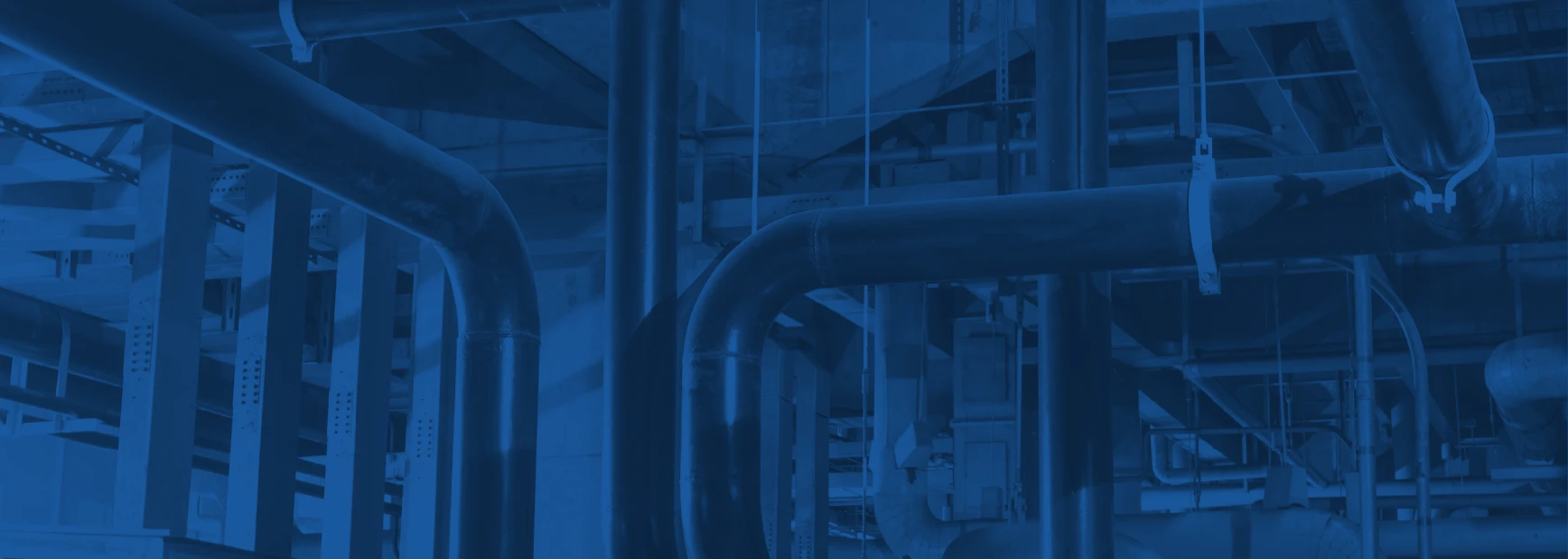
Boiler Blowdown Vessels
ASME Vessels for Intermittent Bottom Boiler Blowdown
Madden Engineered Products is an industry leader in designing and fabricating bottom blowoff vessels. Our company has over 65 years of experience providing cost effective and high quality blowdown set ups for boiler rooms. Helping to ensure operator safety and boiler longevity. Blowing water down from the boiler aids in efficient boiling production, increases equipment service life, and saves on chemical treatment costs.
The standard vessels used in handling this hot, high velocity process are typical called Blowdown Separators and Blowdown Tanks. You can read more about the function and technical differences of these two units here in this blog. You can also click the links below these pictures to visit the individual blowoff vessel web pages.
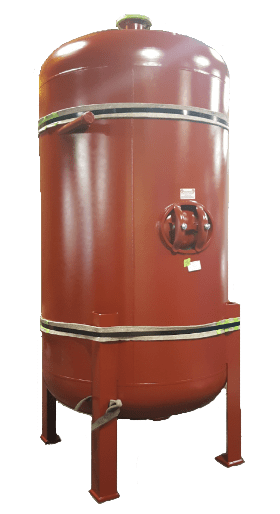
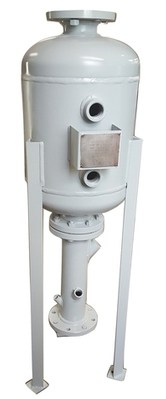
Keeping your boiler(s) free of dissolved solids and other impurities is a pivotal part of the boiling process. We sometimes refer to Tanks and Separators as “necessary evils”. Every boiler should perform intermittent bottom blowdown. With few exceptions, these are required pieces of equipment in the boiler room.
And surprisingly, they often get overlooked. Boiler manufacturers may assume the installing contractor is sourcing it, and vice versa. Only to discover no one had until several weeks before a planned start up.
Madden keeps our most popular blowdown separator models in stock to help combat this semi frequent occurrence. For traditional overflow style blowdown tanks it is not as easy to offer this as almost all are built to order.
When sizing this equipment for your boiler room, the important parameters to consider are:
- Boiler Operating Pressure – the operating pressure of the boiler(s) is the driving factor in sizing most of the connections and capacity of blowdown equipment. We use this value to then calculate the amount of flash steam, remaining condensate, and volume of steam to ensure an adequately sized blowdown vessel is ready to handle the max scenario.
- Boiler blowdown line size – knowing the line size along with the operating pressure ensures we will have very close to exact blowdown parameters. We can use the line size and operating pressure to estimate flow rate into these vessels, and thereby size the rest of the features.
- Boiler Steam Drum size – for water tube boilers using a traditional overflow tank only. This allows us to define an amount of blowdown we want to account for being drained from the boiler. Typically this is a 4″ level drop, sometimes as little as 2″ depending on the situation. We do not need these dimensions for blowdown separators as they are not sized to HOLD a water level, they immediately quench the blowdown with cooling water.
- Boiler Water Capacity – for fire tube boilers. For fire tube boilers, a more precise way to account for expect blowdown amount is to simply look into the specific capacity. Estimating the drum dimensions leaves room for error. In this situation we assume the operator would open the blowdown line for 1 minute maximum. Based on this number we then calculate the holding volume required in the blowdown tank.
To learn more about BLOWDOWN TANKS and BLOWDOWN SEPARATORS click the links here to review their individual web pages.